Jeśli myślałeś, że innowacje w świecie druku należą już do przeszłości, pomyśl jeszcze raz. Joe McEntee wybiera się na interdyscyplinarny spacer po brytyjskim Centrum Badań nad Drukiem
Nie ma wielu środowisk badawczych, w których naukowcy w jednym laboratorium badają zastosowanie grafenu jako podstawy wysokiej jakości odzieży nadającej się do recyklingu; podczas gdy na korytarzu ich rówieśnicy prowadzą kurs starożytnej japońskiej techniki drzeworytu Mokuhanga. Tak jednak właśnie dzieje się w Centrum Badań Druku (CFPR) przy ul University of the West of England (UWE) w Bristolu, gdzie na co dzień zacierają się podziały między sztuką a nauką i przemysłem a środowiskiem akademickim.
Kierując się etosem konwergencji, współpracy i współtworzenia, CFPR jest interdyscyplinarnym przedsięwzięciem skupiającym starszych badaczy, doktorantów, specjalistów technicznych i praktykantów; we wszystkim, od grafiki artystycznej i projektowania, po fizykę, naukę o materiałach i inżynierię. Ich celem jest dostarczanie innowacyjnych rozwiązań dla przyszłości druku poprzez prowadzenie badań empirycznych nad artystycznym, historycznym i przemysłowym znaczeniem kreatywnych praktyk, procesów i technologii drukarskich.
Fizyk stosowany
Warunkiem wstępnym CFPR jest zdolność adaptacji i otwartość na nowe ścieżki badawcze. Weźmy na przykład fizyka stosowanego Zuzanna Klein. Po ukończeniu fizyki medycznej Klein zajął się badaniami optycznymi. Następnie spędziła dwadzieścia lat jako naukowiec zajmujący się badaniami i rozwojem przemysłu w firmie Laboratorium HP w Bristolu, gdzie jej program badawczy obejmował chemię koloidalną, ciekłe kryształy i zaawansowane materiały wyświetlaczowe, a także technologie druku 3D i kryptografię optyczną. Obecnie Klein kieruje pięcioletnim projektem w CFPR. Jego celem jest nowe spojrzenie na różne 1.2th-wiekowe procesy drukowania, aby były tańsze, szybsze i bardziej dostępne.
Jedną z technik, którą Klein studiuje i unowocześnia, jest typ Woodbury, która była pierwszą fotomechaniczną metodą drukowania, która odniosła sukces komercyjny, pozwalającą na odtworzenie ciągłego tonu fotografii. Proces ten, opatentowany w 1864 roku przez brytyjskiego wynalazcę Waltera Woodbury’ego, rozpoczyna się od negatywu „mokrego kolodionu”, co było wówczas stosowaną techniką fotograficzną. Negatyw umieszcza się na warstwie suchej, dwuchromowanej żelatyny i wystawia na światło słoneczne na około 60 minut. Żelatyna, która nie jest wystawiona na działanie światła przez negatyw, pozostaje rozpuszczalna w wodzie i jest po prostu zmywana.
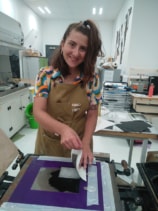
Rezultatem jest zdumiewająco solidna trójwymiarowa płaskorzeźba (forma) obrazu, którą można wcisnąć w ołów za pomocą prasy hydraulicznej. Następnie ołowianą płytę drukarską naoliwia się, wypełnia ciepłą żelatyną pigmentowaną sadzą i przykrywa papierem przed wprowadzeniem do prasy drukarskiej. Po około pięciu minutach papier jest ściągany, a po wyschnięciu atramentu następuje ostateczne spłaszczenie i przycięcie wydruku. Pierwotnie z jednego reliefu żelatynowego można było wykonać do 3 płyt drukarskich, które można było zamontować w karuzeli drukarskiej w celu drukowania masowego.
„Ponieważ wydruki typu Woodbury są oparte na pigmentowanej żelatynie, można je w pełni archiwizować, ponieważ sadza lub sadza są wyjątkowo „odporne na działanie światła”, a żelatyna nie ulegnie zniszczeniu ani nie zmieni się chemicznie, dopóki nie zostanie wystawiona na działanie ekstremalnej wilgoci” – mówi Klein. „Chociaż pierwotny proces jest czasochłonny i stał się przestarzały, gdy na rynku pojawiła się litografia, jakość obrazu jest niezrównana. Nawet dzisiaj typ Woodbury jest jedyną metodą fotomechanicznej reprodukcji ciągłych tonów.
Wracając do tej techniki, Klein i jej współpracownicy opracowali dwie alternatywne metody tworzenia odbitek typu Woodbury przy użyciu nowoczesnych materiałów. „W jednej metodzie” – wyjaśnia Klein – „postępujemy zgodnie z pierwotnym przebiegiem pracy, ale zastępujemy dwuchromowaną żelatynę fotopolimerem, a ołów krzemem”. W ten sposób czas naświetlania ulega skróceniu z 60 minut do sekund, a płyty drukarskie można wykonać w ciągu kilku godzin, a nie dni. Jeszcze szybsza metoda wykorzystuje wycinarkę laserową do tworzenia reliefu w akrylu – na przykład wytwarzając płytę drukarską o wymiarach 10 na 15 cm w 10 minut. Precyzja wycinarki laserowej oznacza również, że warstwy koloru cyjan, magenta, żółty i czarny potrzebne do stworzenia pełnokolorowych obrazów można z łatwością drukować jedna na drugiej.
Obie metody są atrakcyjne dla praktyków sztuk pięknych do tworzenia oryginalnych dzieł sztuki, ale są również interesujące dla firm poszukujących przyjaznego dla środowiska sposobu tworzenia wysokiej jakości reprodukcji fotograficznych na potrzeby instalacji artystycznych i reklam komercyjnych w przestrzeni publicznej. Zaletą jest to, że cięcie laserowe płyt drukarskich jest energooszczędne i prawie nie wytwarza odpadów, a atramenty są na bazie żelatyny (produkt odpadowy przemysłu mięsnego). Co więcej, wydruki ulegają biodegradacji, a atrament można usunąć z papieru poprzez zmycie wodą.
Kolejny obszar badań dla Kleina obejmuje przemysłowe zastosowanie „koloru strukturalnego”, w którym kolor jest generowany nie przez pigmenty, ale przez mikroskopijne wzory odbijające i załamujące światło w unikalny sposób (jak w skrzydłach motyla). Intrygującą opcją jest wprowadzenie dodatkowych warstw cholesterycznych (chiralnych nematycznych) ciekłych kryształów do reliefu typu Woodbury w celu wydrukowania koloru strukturalnego. Przy użyciu odpowiednich materiałów ciekły kryształ można zorientować według warstwy, a oryginalne wydrukowane kolory można zmienić poprzez przyłożenie pola magnetycznego lub elektrycznego, podobnie jak w przypadku wyświetlacza bistabilnego.
Możliwe zastosowania obejmują zapobieganie podrabianiu w przypadku etykietowania towarów luksusowych, mody markowej i produktów farmaceutycznych. „Możliwości komercyjne są tutaj znaczące” – dodaje Klein. „Wyzwanie polega na wyprodukowaniu bezpiecznego opakowania z farbami drukarskimi, które będą zmieniać kolor za każdym razem, gdy produkt zostanie autoryzowany na różnych etapach łańcucha dostaw w drodze do klienta”.
Naukowiec zajmujący się materiałami
Kolega Kleina Nazmul Karim – kierownik badań w ośrodku Laboratorium Aplikacji Grafenu – to kolejny pracownik naukowy, który najwyraźniej jest stworzony na miarę multidyscyplinarnego tygla CFPR. Przed dołączeniem do UWE w 2019 roku Karim spędził cztery lata pracując nad wysokowydajną odzieżą funkcjonalną na bazie grafenu i elektronicznymi tekstyliami do noszenia (e-tekstylia) w firmie Narodowy Instytut Grafenu na University of Manchester, Wielka Brytania.
Jego obecne zainteresowania badawcze – będące częścią zainteresowań CFPR nowy program materiałowy – obejmują przygotowanie grafenu (poprzez eksfoliację i funkcjonalizację), grafenu i innych materiałów 2D do zastosowań w e-tekstyliach. Karim bada również możliwości wytwarzania grafenowych urządzeń do noszenia za pomocą wysoce skalowalnych technik produkcyjnych, takich jak powlekanie i drukowanie (tj. za pomocą „tuszów” grafenowych nakładanych bezpośrednio na tekstylia). „Mój zespół pasjonuje się wprowadzaniem inteligentnych materiałów i sztucznej inteligencji do drukowanej elektroniki na potrzeby nieinwazyjnych, spersonalizowanych zastosowań w opiece zdrowotnej” – mówi Karim.

Najnowsze wyniki grupy, oparte w dużej mierze na pracach prowadzonych przez doktoranta Md. Rashedul Islam, zademonstrować nabieranie kształtu namacalnych możliwości komercyjnych. Islam opracował wszechstronną platformę e-tekstyliów, która jest w całości zadrukowana, ma wysoką przewodność, jest elastyczna i można ją prać w pralce. Materiał może magazynować energię za pomocą drukowanych superkondensatorów grafenowych, monitorując jednocześnie szereg wskaźników fizjologicznych, takich jak tętno, temperatura skóry i różne wskaźniki aktywności. Jeszcze bardziej imponujące jest to, że prototypowy e-tekstylia po przekształceniu w oddzielną opaskę na głowę może rejestrować aktywność mózgu (elektroencefalogram lub EEG) z tym samym standardem, co konwencjonalne sztywne elektrody. Obecnie superkondensatory są ładowane z zewnętrznego źródła zasilania, ale celem jest zapewnienie im w przyszłości samowystarczalności poprzez wprowadzenie funkcji gromadzenia energii.
W procesie produkcyjnym wykorzystuje się wysoce skalowalną technikę sitodruku, w której atrament na bazie grafenu przepuszcza się przez specjalnie zaprojektowaną siatkę na szorstkie i elastyczne podłoże tekstylne. Ścieżki przewodzące są następnie hermetyzowane w celu izolacji i ochrony, tworząc platformę z e-tekstyliów, którą można prać w pralce. Mamy nadzieję, że tego typu sukcesy na wczesnym etapie otworzą drogę do masowej produkcji wielofunkcyjnej odzieży z e-tekstyliów na bazie grafenu, w której każdy element odzieży posiada sieć czujników do noszenia i jest zasilany energią zmagazynowaną w produktach na bazie grafenu superkondensatory tekstylne.
W tym kontekście Laboratorium Aplikacji Grafenu bada zastosowanie grafenu i innych materiałów funkcjonalnych (w tym powłok antybakteryjnych) jako podstawy wysokiej jakości odzieży nadającej się do recyklingu. Obecnie około 55% tekstyliów wytwarza się z syntetycznych poliestrów – najczęściej politereftalanu etylenu (PET), który nie ulega biodegradacji i może pozostawać w środowisku przez setki lat. „Zrozumiałe jest, że marki modowe i sprzedawcy detaliczni coraz bardziej interesują się odejściem od pierwotnego PET na rzecz tkanin poliestrowych na bazie polimerów pochodzących z recyklingu (rPET) o zmniejszonym wpływie na środowisko” – mówi Karim.
Problem w tym, że obecne wersje rPET ulegają starzeniu termicznemu i ulegają degradacji w wyniku przypadkowego zmieszania z innymi materiałami podczas procesu recyklingu. To dopiero początek, zauważa Karim, ale wstępne wyniki CFPR są obiecujące, ponieważ rPET wzmocniony grafenem został już przerobiony na włókna, które są lżejsze, mocniejsze mechanicznie i łatwiejsze do recyklingu. „To będzie długa gra” – dodaje Karim – „będziemy potrzebować trwałej współpracy w całym ekosystemie innowacji. Oznacza to, że grupy akademickie takie jak nasza współpracują z dostawcami grafenu, producentami tekstyliów oraz dużymi sprzedawcami detalicznymi z branży modowej i odzieżowej”.
Projektant ceramiki
Pojawiają się zupełnie inne możliwości produkcyjne Tavsa Jorgensena, garncarz rzemieślniczy i projektant w branży ceramicznej, zanim rozpoczął karierę akademicką. Jorgensen jest w awangardzie wysiłków badawczo-rozwojowych CFPR w produkcja cyfrowa, którego celem jest przyspieszenie dotychczas ograniczonego zastosowania technologii druku 3D, obróbki sterowanej komputerowo i robotyki w produkcji ceramiki.
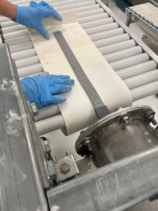
Jorgensen i jego zespół są szczególnie zainteresowani procesem produkcyjnym zwanym wytłaczaniem. Dzieje się tak, gdy miękka i formowalna glina jest przeciskana przez kanał lub „matrycę”, która nadaje materiałowi określony kształt przekroju poprzecznego i daje ciągły liniowy pasek gliny, który można pociąć na kawałki w celu wytworzenia pojedynczych części, takich jak cegły , płytki, okładziny i inne elementy architektoniczne. Wytłaczarki przemysłowe służą do wytwarzania specjalistycznych części ceramicznych, m.in. filtrów do katalizatorów oraz elementów wysokotemperaturowych do pieców i autoklawów. Tymczasem w warsztatach rzemieślniczych często spotyka się ręczne systemy wytłaczania, umożliwiające tworzenie uchwytów i jednorazowych elementów dekoracyjnych wspierających inne metody produkcji, takie jak prasowanie i odlewanie. „Naszym wyzwaniem” – mówi Jorgensen – „jest to, w jaki sposób możemy wykorzystać technologie cyfrowe i robotykę, aby rozszerzyć obecne zastosowania wytłaczania gliny na bardziej innowacyjne zastosowania komercyjne i projektowe”.
Domyślne ustawienie zespołu opiera się w dużej mierze na praktycznych eksperymentach. „Czasami testy przeprowadza się w formie otwartych eksploracji, których wyniki są wysoce nieprzewidywalne, a podejście to opiera się głównie na ciekawości – co się stanie, gdy to zrobimy?” Podstawowe informacje fizyczne i materiałowe są ważnym elementem zrozumienia zachowania gliny. Na przykład podczas suszenia i wypalania wytłaczane kawałki gliny kurczą się o około 10–15%, mogą też wyginać się i pękać pod wpływem naprężeń powstających w procesie wytłaczania.
„Charakter wytłaczania gliny sprawia, że teoretyczne obliczenia wyniku są trudne” – mówi Jorgensen, „chociaż włożono pewne prace w celu opracowania algorytmów, które mogą pomóc przewidzieć przepływ gliny w sytuacji wytłaczania”. W oportunistycznym, interdyscyplinarnym powiązaniu Jorgensen zwrócił się do specjalistycznej wiedzy: Damien Lech – były fizyk teoretyczny CFPR, obecnie pracujący w belgijskim centrum nanoelektroniki Imec – opracowanie modeli przewidywających, jak konkretna geometria matrycy może wpłynąć na ciśnienie potrzebne do wytłaczania gliny. „Chociaż podstawową metodologią badań pozostają testy empiryczne” – dodaje Jorgensen, „modelowanie teoretyczne okazało się nieocenione, zapewniając podstawową wiedzę na temat tego, które geometrie najlepiej nadają się do zastosowania w rzeczywistych eksperymentach fizycznych”.

Zespół tworzy także przepływy pracy oprzyrządowania, które umożliwiają szybkie prototypowanie i testowanie nowatorskich projektów matryc do druku 3D, co otwiera możliwości zastosowań wytłaczania ceramiki w wysokowydajnych zastosowaniach przemysłowych. Najważniejszym elementem jest współpraca badawczo-rozwojowa CFPR z Narodowe Centrum Kompozytów (NCC) w Bristolu. Interesują ich możliwości wytłaczania kompozytów z osnową ceramiczną (CMC), klasy materiałów, w których pasta ceramiczna jest mieszana z nieorganicznymi spoiwami w celu zwiększenia odporności na pękanie pod obciążeniem mechanicznym lub termomechanicznym.
Partnerzy CFPR/NCC obecnie definiują i iterują specyfikę procesu – w tym narzędzia pomocnicze, przyrządy, komponenty i przepływy pracy. Jednak w perspektywie długoterminowej rozważają wszelkiego rodzaju zastosowania w sektorach takich jak wytwarzanie energii i przemysł lotniczy, gdzie CMC są coraz częściej stosowane w wysokotemperaturowych systemach osłon cieplnych. „Wytłaczanie to całkowicie nowatorski sposób wytwarzania CMC” – mówi Jorgensen, „a badania te otwierają przed nami możliwość tworzenia części CMC o egzotycznych geometriach, takich jak rury i profile o złożonej strukturze wewnętrznej”. Takie rury CMC cieszą się zainteresowaniem w elektrowniach jądrowych nowej generacji, podczas gdy proces wytłaczania może wesprzeć brytyjski cel zerowej emisji dwutlenku węgla netto w przypadku materiałów budowlanych, przy czym Jorgensen i współpracownicy badają wytłaczanie niewypalonej gliny i mieszanek włókien w celu uzyskania niskiej węglowe elementy budowlane.
Otwarty sposób myślenia i otwarty na biznes
Jeśli konwergencja, współpraca i współtworzenie mają fundamentalne znaczenie dla modelu badawczego CFPR, tak samo jest z połączeniem artystów, projektantów, naukowców i technologów, pracujących w obu dyscyplinach druku tradycyjnego i cyfrowego.
Grupa zrzesza także ludzi z różnych środowisk, badaczy z przemysłu i środowisk akademickich. To połączenie wiedzy specjalistycznej i doświadczenia wspiera szeroką międzynarodową współpracę akademicką i przemysłową CFPR; z partnerami handlowymi, w tym specjalistycznymi drukarniami, producentami ceramiki i międzynarodowymi firmami technologicznymi. Wspólne projekty badawczo-rozwojowe obejmują ukierunkowane badania kontraktowe i studia wykonalności, aż po wspólne opracowywanie zaawansowanych materiałów, procesów i pełnych systemów drukowania.
Oczywiste jest, że nie ma sztywnych zasad współpracy w CFPR, a raczej wariacje na temat, w których otwarte myślenie łączy się z kreatywnością, innowacjami naukowymi i technologicznymi w zaawansowanych praktykach drukarskich.