Physicists in Israel have printed a micro-optical element that generates a twisted Bessel beam on the end of an optical fibre. The polymer device consists of a parabolic lens for light collimation and a helical axicon that twists the light. According to the researchers, their work demonstrates how elements that can generate sophisticated beam shapes can be integrated into optical fibres. Such devices could provide tailored light beams for a variety of optical technologies.
A wide range of applications – including communications, sensing and imaging, for example – rely on optical fibres. Light exiting these fibres is usually manipulated and steered using large optical elements. Micro-optics is seen as a way to reduce the size of these elements, expand their function and cut costs. Integrating them directly onto optical fibres could be particularly advantageous.
Shaping light into Bessel beams, a type of twisted light that carries orbital angular momentum, is beneficial due to their resistance to diffraction and large depth of focus. These are promising characteristics for various applications such as optical tweezers and material processing.
“The ability to create a Bessel beam directly from an optical fibre could be used for particle manipulation or fibre-integrated stimulated emission depletion microscopy, a technique that produces super-resolution images,” explains Shlomi Lightman, at the Soreq Nuclear Research Center.
Bessel beams are often created by focusing a Gaussian beam through a cone-shaped lens known as an axicon. Although complex optical elements like axicons have been added to optical fibres before, Lightman and colleagues say that the fabrication processes are challenging. To simplify the process and reduce fabrication time they turned to 3D direct laser writing (3D-DLW).
In 3D-DLW, a photosensitive material is polymerized via a two-photon absorption process using a femtosecond laser. As only the tiny areas where two-photon absorption occurs turn solid, the technique enables the creation of high-resolution 3D elements.
The team printed a 110 µm high, 60 µm diameter optical device on the end of an optical fibre. The device included a parabolic lens with a 27 µm focal length and an axicon with a cone of radius 30 µm and a height of 23 µm. The parabolic lens was designed to align the widely diffracted light from the fibre and focus it into the helical axicon. The axicon had a helical structure designed to add orbital angular momentum to the light.
Once the device was printed, a process that took around four minutes, the researchers spliced the fibre containing the micro-optical device to a fibre laser. They then tested its performance using a purpose-built optical measuring system.
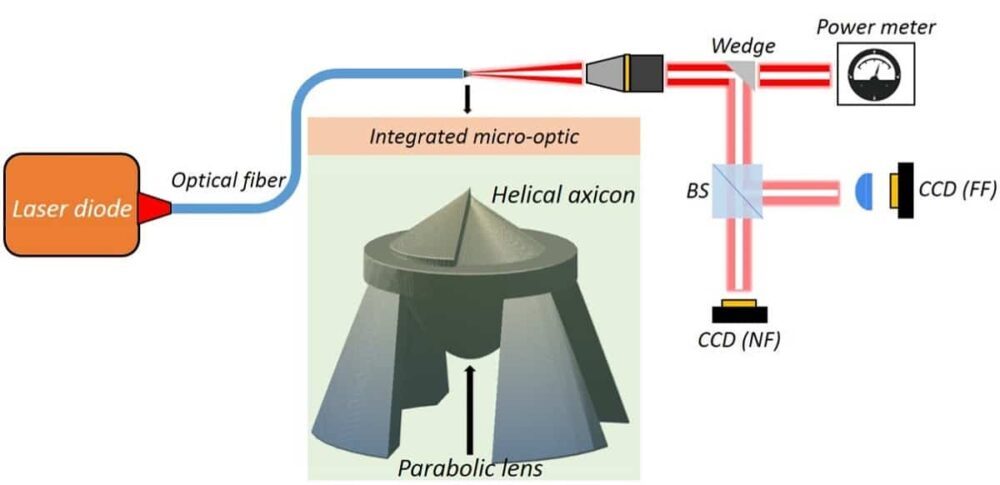
They found that the device generated a Gaussian–Bessel beam with an initial width of 10 µm. Along a 2 mm distance, this expanded to a width of 30 µm. According to the researchers, a Gaussian beam with identical initial width will reach a width of 270 µm over the same distance, demonstrating that the beam produced by their device is a diffracting-free beam.
The beam of light produced by the micro-optical element was also found to have an orbital angular momentum value of 1 ħ per photon, as expected. The incoming laser beam had no orbital angular momentum.
New devices produce and detect twisted light
As the device was printed from organic photosensitive polymers, the researchers were concerned that it may suffer laser-induced damage and limited mechanical stability over time. When they gradually increased the laser power to a maximum optical density of 3.8 MW/cm2 there was no obvious impact on the beam properties. They are now, however, experimenting with this 3D-DLW method on hybrid photosensitive materials that contain a low percentage of polymer. Optical elements printed from such materials could have longer shelf lives and be more resistance to high laser powers, they say.
The team notes that this laser printing technique could also be used for other optical devices. “Our fabrication method could also be used to upgrade an inexpensive lens to a higher quality smart lens by printing a smart small structure on it,” Lightman says.
The researchers report their results in Optics Letters.