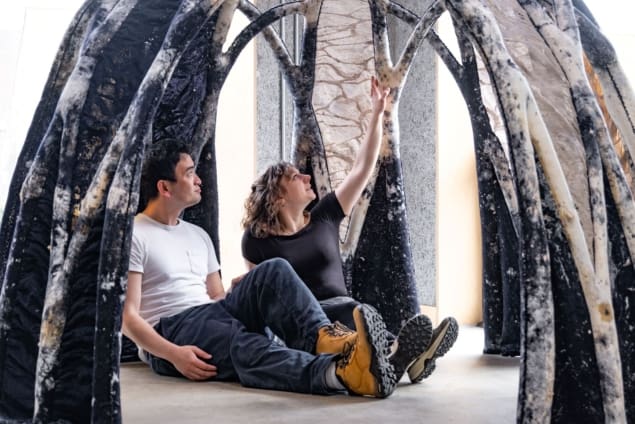
Most people strive to keep fungus out of their homes. Now, however, two groups of materials researchers are exploring ways to weave it into the very fabric of buildings.
The first group, led by textile scientist Jane Scott at Newcastle University in the UK, created knitted structures that hold fungal strands called mycelium in place while the fungus grows. The result is a lightweight composite material that could be used to build strong, eco-friendly structures.
The second group, led by nanoengineer Everson Kandare and biotechnologist Tien Huynh of RMIT University in Melbourne, Australia, used mycelium to create compressed sheets of fire-retardant material. The hope is that such sheets could replace flammable cladding panels like the ones that contributed to the deadly Grenfell Tower fire, which killed 72 Londoners in 2017.
Charring fungus has a protective effect
For Kandare, Huynh and colleagues, the source of mycelium’s appeal lies in the way it behaves when exposed to fire and other sources of radiant heat. Instead of bursting into flames, as the Grenfell cladding did, an exposed surface made of mycelium decomposes to form a gritty black substance called char. This layer of char has a two-part protective effect. As well as slowing down the transfer of heat, it prevents volatile materials in the layers beneath it from escaping into the combustion zone.

A further benefit is that when mycelium does burn, it produces only carbon dioxide and water. This is in stark contrast to commercial fire retardants, Huynh tells Physics World. “Currently there are halogenated and non-halogenated fire retardants that have health and environmental concerns,” she explains. “These include bromide and chlorine (halogenated) or phosphorus and nitrogen (non-halogenated) based fire retardants, and when they burn [they] produce toxins.”
Working with the mushroom industry
In the latest study, which is published in the journal Polymer Degradation and Stability, the RMIT team worked with colleagues at the University of New South Wales and the Hong Kong Polytechnic University to develop a way of growing sheets of pure mycelium. The results resemble toast-coloured cardboard, and Huynh says the easiest way to incorporate into buildings would be to add it to existing materials like a wallpaper. “It’s light, flexible and versatile so would suit multiple applications used in the building industry,” she says.
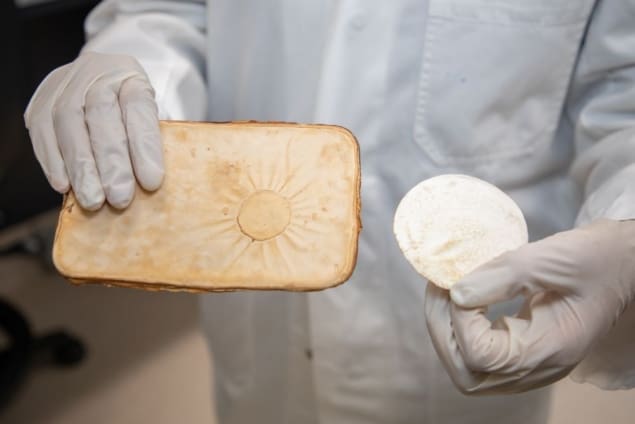
While the RMIT team grew its mycelium sheets from a culture of inedible bracket fungus, Ganoderma australe, Huynh says it should also be possible to produce the sheets from waste generated by commercial mushroom growers. “Creation of these fungal products uses molasses, which is an agricultural waste from the sugarcane industry,” she explains. “Given that [the world] produced ~177 million metric tonnes of sugar in 2022-2023, this is a significant contribution for waste reduction.”
Knitting supports for mycelium structures
Sustainability and waste reduction are also motivating factors for Scott and her colleagues at Newcastle and the Vrije Universiteit Brussel in Belgium. Writing in the journal Frontiers in Bioengineering and Biotechnology, they note that the excellent thermal and acoustic properties of mycelium composites give them “huge potential” as inexpensive replacements for foams, timber and plastics in building interiors. The challenge, they write, is to grow these composites in a way that is scalable and makes complex shapes possible, while still meeting requirements for structure and stability.
To make mycelium composites, scientists typically begin by mixing fungal spores with grain (a food source) and materials such as sawdust and cellulose (a substrate for the fungus to grow on). The next step is to pack the mixture into a mould and place it in a warm, dark and humid environment. Under these conditions, the mycelium grows relatively quickly, binding the substrate together with its filamentous, root-like structures. Once the composite reaches the desired density, the growth process is halted and the material dried out so that it doesn’t produce mushrooms.
The problem with this is that mycelium needs oxygen to grow, and this requirement restricts the size and shape of the moulds (in the manufacturing sense of the word, not the fungal one) it can grow in. Or at least, it does if the moulds are solid. As an alternative, Scott drew on her textiles training to design a mycelium mixing and production system based on moulds knitted from strong but air-permeable merino wool.
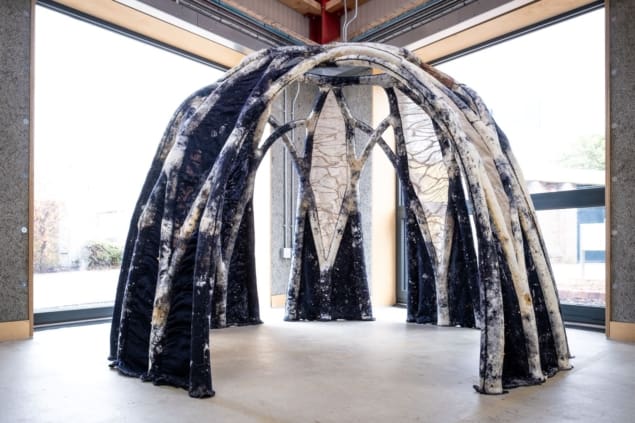
“We are an interdisciplinary group of researchers including expertise in 3D knit programming and manufacture, so we have been able to bring together quite unique skillsets to produce this work,” she tells Physics World. “The major advantage of knitting technology compared to other textile processes is the ability to knit 3D structures and forms with no seams and no waste.”
Once the knitted moulds were complete, Scott and colleagues sterilized them and attached them to a rigid structure to support the mycelium concrete, or myocrete, as it grew. They then used an injection gun to fill the moulds with a smooth, viscous paste containing paper powder, paper fibre clumps, water, glycerine and xanthan gum as well as fungal spores. “This consistency is required when working with 3D knitted formwork, which is versatile and structurally efficient,” Scott says. “The difficulty is in bringing both components together to prototype at an architectural scale.”
Mouldy materials of the future
The team’s first prototype, created in 2022, provides a vivid demonstration of myocrete’s capabilities (see photo). Known as BioKnit, this 1.8m high, 2m diameter freestanding structure is made entirely of myocrete and was grown as a unit, meaning it contains no joins that could become weak points. A second prototype, entitled The Living Room, contains a mixture of mycelium spores, wool from hardy Herdwick sheep, and a mix of sawdust and wastepaper from local mills.
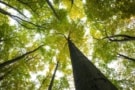
Processed wood can be moulded into complex 3D structures
For mould-averse consumers, the colours of BioKnit and The Living Room may be a little off-putting – the surfaces bear a strong resemblance to something you might spray with bleach – but Scott notes that different colours and finishes could transform the myocrete’s appearance. In any case, she believes the material’s advantages can overcome any resistance. “The aesthetic is new and different, [but] what we find compelling about this process is the ability to produce new shapes and forms that could help us transform interior spaces,” she says. “Our work includes some of the most common materials and processes, such as wool and knitting, and I think this offers consumers a way to understand mycelium through the lens of something familiar like textiles.”
- SEO Powered Content & PR Distribution. Get Amplified Today.
- PlatoData.Network Vertical Generative Ai. Empower Yourself. Access Here.
- PlatoAiStream. Web3 Intelligence. Knowledge Amplified. Access Here.
- PlatoESG. Automotive / EVs, Carbon, CleanTech, Energy, Environment, Solar, Waste Management. Access Here.
- BlockOffsets. Modernizing Environmental Offset Ownership. Access Here.
- Source: https://physicsworld.com/a/why-fungi-could-hold-the-key-to-eco-friendly-fire-resistant-buildings/
- :has
- :is
- :not
- 1
- 2000
- 2017
- 2022
- 2023
- 3d
- 7
- 72
- a
- ability
- Able
- About
- AC
- add
- ADvantage
- advantages
- Agricultural
- also
- alternative
- an
- and
- Another
- any
- appeal
- applications
- architectural
- ARE
- AS
- At
- Australia
- background
- based
- BE
- Bear
- become
- been
- begin
- Belgium
- believes
- beneath
- benefit
- binding
- biotechnology
- Black
- both
- bring
- Bringing
- build
- Building
- built
- burn
- but
- by
- called
- camera
- Campus
- CAN
- capabilities
- carbon
- carbon dioxide
- case
- challenge
- click
- colleagues
- commercial
- Common
- compared
- compelling
- complete
- complex
- components
- Concerns
- conditions
- Consumers
- contains
- contrast
- contributed
- contribution
- could
- create
- created
- Culture
- Dark
- Design
- desired
- develop
- different
- Difficulty
- does
- Doesn’t
- down
- easiest
- Eco-friendly
- effect
- efficient
- entirely
- entitled
- Environment
- environmental
- environmental concerns
- excellent
- existing
- expertise
- Explains
- Exploring
- exposed
- fabric
- factors
- familiar
- fill
- Find
- Fire
- First
- flexible
- food
- For
- forest
- form
- formed
- forms
- from
- full
- further
- generated
- Give
- Group
- Group’s
- Grow
- Growing
- grown
- Grows
- Growth
- Hands
- Have
- Health
- help
- her
- High
- hold
- Homes
- Hong
- Hong Kong
- hope
- However
- HTML
- http
- HTTPS
- Hub
- humid
- i
- if
- image
- in
- include
- includes
- Including
- incorporate
- industry
- information
- inside
- instead
- interior
- into
- issue
- IT
- ITS
- Joins
- journal
- jpg
- Keep
- Key
- knit
- known
- Kong
- lab
- largest
- latest
- layer
- layers
- least
- Led
- lies
- light
- lightweight
- like
- little
- living
- local
- made
- major
- make
- MAKES
- manufacturing
- material
- materials
- max-width
- May..
- meaning
- meeting
- Melbourne
- metric
- might
- million
- mix
- Mixing
- mixture
- most
- multiple
- Mycelium
- needs
- New
- New South Wales
- next
- no
- Notes
- now
- of
- off
- Offers
- on
- once
- ONE
- ones
- only
- open
- opening
- or
- Other
- out
- Overcome
- Oxygen
- Pack
- panels
- Paper
- People
- photo
- Physics
- Physics World
- Place
- plastics
- plato
- Plato Data Intelligence
- PlatoData
- points
- possible
- prevents
- Problem
- process
- processes
- produce
- produces
- Production
- Products
- Programming
- properties
- Protective
- prototype
- provides
- published
- quickly
- Radiant
- Reaches
- reduction
- Regulation
- relatively
- replace
- required
- requirement
- Requirements
- research
- researchers
- resembles
- Resistance
- result
- Results
- rigid
- Room
- same
- says
- scalable
- Scale
- Scientist
- scientists
- scott
- Second
- see
- sense
- Shape
- shapes
- she
- sheep
- sheet
- shelves
- should
- Shows
- significant
- Sitting
- Size
- Slowing
- smooth
- So
- Soft
- solid
- some
- something
- Source
- Sources
- South
- spaces
- Stability
- stark
- Step
- Still
- Strands
- strive
- strong
- structure
- Student
- Study
- substance
- such
- Suit
- support
- Supports
- Surface
- system
- team
- Technology
- tells
- textiles
- that
- The
- the hub
- The Source
- the UK
- the world
- their
- Them
- then
- There.
- thermal
- These
- they
- think
- this
- Through
- thumbnail
- to
- together
- towards
- Tower
- Training
- transfer
- Transform
- Trees
- true
- two
- typically
- Uk
- under
- understand
- unique
- unit
- university
- us
- used
- uses
- versatile
- very
- View
- volatile
- warm
- was
- Waste
- Water
- Way..
- ways
- we
- Weave
- WELL
- were
- What
- when
- which
- while
- why
- Wikipedia
- with
- wood
- Word
- Work
- worked
- working
- world
- would
- write
- writing
- You
- zephyrnet