Si pensaba que la innovación en el mundo de la impresión era cosa del pasado, piénselo de nuevo. Joe McEntee realiza un paseo multidisciplinario por el Centro de Investigación de la Impresión del Reino Unido
No puede haber muchos entornos de investigación en los que los científicos de un laboratorio estén investigando el uso de grafeno como base para ropa reciclable de alta calidad; mientras que a lo largo del pasillo sus compañeros imparten un curso sobre la antigua técnica japonesa de impresión en madera Mokuhanga. Sin embargo, eso es exactamente lo que sucede en el Centro de Investigación de Impresión (CFPR) en el Universidad del Oeste de Inglaterra (UWE) en Bristol, donde las divisiones entre artes, ciencias e industria-académica se salvan a diario.
Siguiendo un espíritu de convergencia, colaboración y cocreación, el CFPR es una empresa interdisciplinaria que reúne a investigadores senior, posgraduados, especialistas técnicos y aprendices; en todo, desde impresión artística y diseño hasta física, ciencia de materiales e ingeniería. Su objetivo es ofrecer soluciones innovadoras para el futuro de la impresión mediante la realización de investigaciones empíricas sobre la importancia artística, histórica e industrial de las prácticas, procesos y tecnologías de impresión creativa.
El físico aplicado.
La adaptabilidad y la apertura a nuevas vías de investigación son requisitos previos en el CFPR. Tomemos, por ejemplo, física aplicada. susanne klein. Habiendo estudiado física médica, Klein pasó a la investigación óptica. Luego pasó dos décadas como científica de I+D industrial en Laboratorios HP en Bristol, donde su programa de investigación abarcó desde química coloidal, cristales líquidos y materiales de visualización avanzados hasta tecnologías de impresión 3D y criptografía óptica. Ahora, Klein lidera un proyecto de cinco años en el CFPR. Financiado con una suma de £1.2 millones, su objetivo es reimaginar varios 19thprocesos de impresión del siglo XIX para hacerlos más baratos, más rápidos y más accesibles.
Una técnica que Klein está estudiando y modernizando es el tipo Woodbury., que fue el primer método de impresión fotomecánica comercialmente exitoso para reproducir el tono continuo de las fotografías. Patentado en 1864 por el inventor británico Walter Woodbury, el proceso comienza con un negativo de “colodión húmedo”, que era la técnica fotográfica utilizada en aquella época. El negativo se coloca sobre una capa de gelatina dicromada seca y se expone al sol durante unos 60 minutos. Cualquier gelatina que no se exponga a la luz a través del negativo sigue siendo soluble en agua y simplemente se elimina con el lavado.
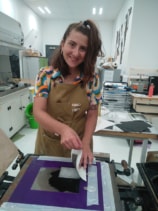
El resultado es un relieve 3D (un molde) sorprendentemente robusto de la imagen, que se puede prensar para convertirlo en plomo mediante una prensa hidráulica. Luego se engrasa la plancha de plomo, se llena con una gelatina tibia pigmentada con hollín y se cubre con papel antes de pasar a la imprenta. Después de unos cinco minutos, se retira el papel y, una vez que la tinta está seca, finalmente se aplana y recorta la impresión. Originalmente, a partir de un único relieve de gelatina se podían fabricar hasta 10 planchas de impresión, que se podían montar en un carrusel de impresión para la impresión en masa.
“Dado que las impresiones tipo Woodbury se basan en gelatina pigmentada, se pueden archivar por completo porque el hollín o el negro de humo son extremadamente resistentes a la luz y la gelatina no se deteriora ni cambia químicamente siempre que no se exponga a una humedad extrema”, dice Klein. “Aunque el proceso original lleva mucho tiempo y quedó obsoleto cuando despegó la litografía, la calidad de la imagen es insuperable. Incluso hoy en día, Woodburytype sigue siendo el único método de reproducción fotomecánica de tonos continuos”.
Al revisar la técnica, Klein y sus colegas han desarrollado dos rutas alternativas para crear impresiones tipo Woodbury con materiales modernos. "En un método", explica Klein, "seguimos el flujo de trabajo original, pero reemplazamos la gelatina dicromada con fotopolímero y el plomo con silicio". De esta manera, el tiempo de exposición se reduce de 60 minutos a segundos, mientras que las planchas de impresión se pueden fabricar en horas en lugar de días. Un método aún más rápido utiliza un cortador láser para crear un relieve en acrílico, produciendo una plancha de impresión de 10 por 15 cm en 10 minutos, por ejemplo. La precisión del cortador láser también significa que las capas de cian, magenta, amarillo y negro necesarias para crear imágenes a todo color se pueden imprimir fácilmente una encima de otra.
Ambos métodos resultan atractivos para los profesionales de las bellas artes para la creación de obras de arte originales, pero también son interesantes para las empresas que buscan una forma respetuosa con el medio ambiente de crear reproducciones fotográficas de alta calidad para instalaciones artísticas y publicidad comercial en espacios públicos. Las ventajas son que el corte por láser de planchas de impresión es energéticamente eficiente y casi no produce residuos, mientras que las tintas son a base de gelatina (un producto de desecho de la industria procesadora de carne). Además, las impresiones son biodegradables y la tinta se puede quitar del papel lavándolo con agua.
Otra área de investigación Para Klein implica la aplicación industrial del “color estructural”, donde el color no es generado por pigmentos sino por patrones microscópicos que reflejan y refractan la luz de maneras únicas (como en las alas de una mariposa). Una opción interesante es introducir capas adicionales de cristales líquidos colestéricos (nemáticos quirales) en el relieve de un tipo Woodbury, para imprimir color estructural. Con los materiales adecuados, el cristal líquido podría orientarse por la capa y cambiar los colores impresos originales aplicando un campo magnético o eléctrico, no muy diferente a una pantalla biestable.
Las posibles aplicaciones incluyen la lucha contra la falsificación para el etiquetado de artículos de lujo, moda de diseñador y productos farmacéuticos. "La oportunidad comercial aquí es significativa", añade Klein. "El desafío es producir envases seguros con tintas de impresión que cambien de color cada vez que se autoriza un artículo en diferentes etapas de la cadena de suministro en su camino hacia el cliente".
El científico de materiales
colega de klein Nazmul Karim – líder de investigación en el centro Laboratorio de Aplicación de Grafeno – es otro académico aparentemente hecho a medida para el crisol multidisciplinario del CFPR. Antes de unirse a la UWE en 2019, Karim pasó cuatro años trabajando en ropa funcional de alto rendimiento a base de grafeno y textiles electrónicos portátiles (e-textiles) en la Instituto Nacional de Grafeno en el Universidad de Manchester, REINO UNIDO.
Sus intereses de investigación actuales, que forman parte del CFPR nuevo programa de materiales – incluir la preparación de grafeno (mediante exfoliación y funcionalización), grafeno y otros materiales 2D para aplicaciones de textiles electrónicos. Karim también está estudiando cómo fabricar dispositivos portátiles de grafeno mediante técnicas de fabricación altamente escalables, como el recubrimiento y la impresión (es decir, con “tintas” de grafeno aplicadas directamente sobre los textiles). "A mi equipo le apasiona introducir materiales inteligentes e inteligencia artificial en la electrónica impresa para aplicaciones de atención sanitaria personalizadas y no invasivas", afirma Karim.

Los últimos resultados del grupo, basados en gran medida en el trabajo realizado por el estudiante de doctorado Md. Rashedul Islam, demuestran la oportunidad comercial tangible que está tomando forma. Islam ha desarrollado una plataforma versátil de textiles electrónicos que está completamente impresa, es altamente conductora, flexible y se puede lavar a máquina. El material puede almacenar energía utilizando supercondensadores de grafeno impresos mientras monitorea una variedad de indicadores fisiológicos, como la frecuencia cardíaca, la temperatura de la piel y una variedad de métricas de actividad. Aún más impresionante es que, cuando se le da forma de diadema separada, el prototipo de tejido electrónico puede registrar la actividad cerebral (un electroencefalograma o EEG) con el mismo estándar que los electrodos rígidos convencionales. Por el momento, los supercondensadores se cargan mediante una fuente de energía externa, pero el objetivo es hacerlos autosuficientes en el futuro mediante la introducción de la función de recolección de energía.
El proceso de fabricación aprovecha una técnica de serigrafía altamente escalable, en la que la tinta a base de grafeno pasa a través de una malla diseñada a medida sobre un sustrato textil rugoso y flexible. Luego, las pistas conductoras se encapsulan para aislamiento y protección, para producir una plataforma de textiles electrónicos lavable a máquina. La esperanza es que éxitos iniciales como este abran el camino a la producción en volumen de prendas textiles electrónicas multifuncionales basadas en grafeno, en las que cada prenda tiene una red de sensores portátiles y funciona con la energía almacenada en grafeno. Supercondensadores textiles.
En un frente relacionado, el Laboratorio de Aplicaciones de Grafeno está investigando el uso de grafeno y otros materiales funcionales (incluidos recubrimientos antimicrobianos) como base para prendas reciclables de alta calidad. En la actualidad, alrededor del 55% de los textiles están hechos de poliésteres sintéticos, más comúnmente tereftalato de polietileno (PET), que no es biodegradable y puede permanecer en el medio ambiente durante cientos de años. "Es comprensible que las marcas de moda y los minoristas estén cada vez más interesados en pasar del PET virgen a tejidos de poliéster a base de polímeros reciclados (rPET) con un impacto medioambiental reducido", afirma Karim.
El problema es que las versiones actuales de rPET sufren envejecimiento térmico y se degradan como resultado de la mezcla aleatoria con otros materiales durante el proceso de reciclaje. Todavía es pronto, señala Karim, pero los resultados iniciales del CFPR son prometedores: el rPET mejorado con grafeno ya se ha hilado para obtener fibras que son más ligeras, mecánicamente más robustas y más fáciles de reciclar. “Será un proceso largo”, añade Karim, “y necesitaremos una colaboración sostenida en todo el ecosistema de innovación. Eso significa que grupos académicos como el nuestro trabajan mano a mano con proveedores de grafeno, fabricantes textiles y los grandes minoristas de moda y ropa”.
El diseñador cerámico
Una oportunidad de fabricación completamente diferente preocupa Tavs Jorgensen, alfarero artesanal y diseñador en la industria de la cerámica antes de seguir una carrera en el mundo académico. Jorgensen está a la vanguardia de los esfuerzos de I+D de CFPR en fabricación digital, con el objetivo de acelerar la hasta ahora limitada aplicación de las tecnologías de impresión 3D, el mecanizado controlado por ordenador y la robótica en la producción cerámica.
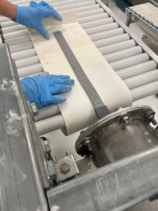
Jorgensen y su equipo están particularmente interesados en un proceso de producción conocido como extrusión. Esto ocurre cuando se fuerza arcilla blanda y moldeable a través de un canal, o "troquel", que imparte una forma transversal particular al material y produce una tira de arcilla lineal continua que se puede cortar en pedazos para producir piezas individuales, como ladrillos. , azulejos, revestimientos y otros componentes arquitectónicos. Las extrusoras industriales se utilizan para fabricar piezas cerámicas especializadas, incluidos filtros para convertidores catalíticos y componentes de alta temperatura para hornos y autoclaves. Mientras tanto, en los talleres artesanales se encuentran a menudo sistemas de extrusión manuales para crear mangos y elementos decorativos únicos que complementan otros métodos de producción, como el prensado y la fundición. "Nuestro desafío", dice Jorgensen, "es cómo podemos explotar las tecnologías digitales y la robótica para extender los usos actuales de la extrusión de arcilla a aplicaciones comerciales y de diseño más innovadoras".
La configuración predeterminada del equipo se basa en gran medida en experimentos prácticos. "A veces las pruebas se llevan a cabo como exploraciones abiertas con resultados muy impredecibles, un enfoque impulsado en gran medida por la curiosidad: ¿qué sucede cuando hacemos esto?" Los conocimientos físicos y materiales fundamentales son un elemento importante para comprender cómo se comporta la arcilla. Por ejemplo, durante el secado y la cocción, las piezas de arcilla extruida se encogen entre un 10% y un 15% y pueden doblarse y agrietarse debido a las tensiones del proceso de extrusión.
"La naturaleza de la extrusión de arcilla dificulta los cálculos teóricos del resultado", dice Jorgensen, "aunque se ha trabajado algo para desarrollar algoritmos que puedan ayudar a predecir el flujo de arcilla en una situación de extrusión". En una alianza interdisciplinaria oportunista, Jorgensen recurrió a la experiencia de Damien Leech – ex físico teórico del CFPR que ahora trabaja en el centro belga de nanoelectrónica imec – desarrollar modelos que predigan cómo determinadas geometrías de matrices podrían afectar las presiones necesarias para extruir arcilla. "Si bien las pruebas empíricas siguen siendo la metodología central de las investigaciones", añade Jorgensen, "el modelado teórico ha demostrado ser invaluable, ya que proporciona una comprensión básica de qué geometrías se implementarían mejor en los experimentos físicos del mundo real".

El equipo también está creando flujos de trabajo de herramientas que permiten crear prototipos y probar rápidamente nuevos diseños de troqueles para impresión 3D, lo que está abriendo aplicaciones para la extrusión de cerámica en aplicaciones industriales de alto rendimiento. Al frente y al centro está la colaboración de I+D de CFPR con el Centro Nacional de Composites (NCC) en Bristol. Están interesados en el potencial de extrusión de compuestos de matriz cerámica (CMC), una clase de materiales en los que la pasta cerámica se mezcla con aglutinantes inorgánicos para aumentar la tenacidad a la fractura bajo carga mecánica o termomecánica.
Los socios de CFPR/NCC actualmente están definiendo e iterando los detalles del proceso, incluidas las herramientas de soporte, plantillas, componentes y flujos de trabajo. Sin embargo, a largo plazo están considerando todo tipo de aplicaciones en sectores como la generación de energía y el aeroespacial, donde los CMC se utilizan cada vez más para sistemas de protección térmica de alta temperatura. "La extrusión es una forma completamente nueva de producir CMC", dice Jorgensen, "y esta investigación nos abre la oportunidad de crear piezas de CMC con geometrías exóticas, como tuberías y perfiles con estructuras internas complejas". Estos tubos de CMC están atrayendo interés para la próxima generación de centrales nucleares, mientras que el proceso de extrusión tiene el potencial de respaldar el objetivo de carbono neto cero del Reino Unido para materiales de construcción. Jorgensen y sus colegas exploran la extrusión de mezclas de arcilla y fibras sin cocer para obtener bajas emisiones de carbono. componentes de construcción de carbono.
Una mentalidad abierta y abierta a los negocios.
Si la convergencia, la colaboración y la cocreación son fundamentales para el modelo de investigación del CFPR, también lo es la combinación de artistas, diseñadores, científicos y tecnólogos del centro, que trabajan en disciplinas de impresión tanto tradicionales como digitales.
El grupo también reúne a personas de diversos orígenes, con investigadores de la industria y del mundo académico. Esta combinación de conocimientos y experiencia respalda las amplias colaboraciones académicas e industriales internacionales del CFPR; con socios comerciales que incluyen imprentas especializadas, fabricantes de cerámica y firmas tecnológicas multinacionales. Los proyectos conjuntos de I+D abarcan desde investigaciones por contrato específicas y estudios de viabilidad hasta el desarrollo conjunto de materiales, procesos y sistemas de impresión completos avanzados.
Es evidente que no existe un reglamento estricto sobre la colaboración en el CFPR, sino más bien variaciones sobre un tema en el que el pensamiento abierto se combina con la creatividad, la ciencia y la innovación tecnológica en prácticas de impresión avanzadas.