Si vous pensiez que l’innovation dans le monde de l’imprimerie appartenait au passé, détrompez-vous. Joe McEntee part pour une promenade multidisciplinaire au Centre for Print Research du Royaume-Uni
Il ne peut pas y avoir beaucoup d’environnements de recherche où les scientifiques d’un laboratoire étudient l’utilisation du graphène comme base de vêtements recyclables de haute qualité ; tandis que, le long du couloir, leurs pairs donnent un cours sur l'ancienne technique japonaise d'impression sur bois, Mokuhanga. Or, c’est exactement ce qui se passe au Centre de recherche sur l'impression (CFPR) au Université de l'Ouest de l'Angleterre (UWE) à Bristol, où les clivages arts-sciences et industrie-université sont comblés quotidiennement.
Suivant une philosophie de convergence, de collaboration et de co-création, le CFPR est une entreprise interdisciplinaire qui rassemble des chercheurs seniors, des étudiants de troisième cycle, des spécialistes techniques et des apprentis ; dans tous les domaines, de la gravure et du design d'art à la physique, à la science des matériaux et à l'ingénierie. Leur objectif est de proposer des solutions innovantes pour l’avenir de l’impression en menant des enquêtes empiriques sur l’importance artistique, historique et industrielle des pratiques, processus et technologies d’impression créative.
Le physicien appliqué
L'adaptabilité et l'ouverture aux nouvelles voies de recherche sont des prérequis au CFPR. Prenons, par exemple, un physicien appliqué Susan Klein. Après avoir étudié la physique médicale, Klein s'est tourné vers la recherche optique. Elle a ensuite passé deux décennies en tant que scientifique en R&D industrielle chez Laboratoires HP à Bristol, où son programme de recherche s'étendait de la chimie colloïdale, des cristaux liquides et des matériaux d'affichage avancés aux technologies d'impression 3D et à la cryptographie optique. Aujourd'hui, Klein dirige un projet de cinq ans au CFPR. Financé à hauteur de 1.2 million de livres sterling, son objectif est de réinventer divers 19thprocessus d'impression du siècle pour les rendre moins chers, plus rapides et plus accessibles.
Une technique que Klein étudie et modernise est le Woodburytype., qui fut la première méthode d'impression photomécanique commercialement réussie pour reproduire le ton continu des photographies. Breveté en 1864 par l'inventeur britannique Walter Woodbury, le procédé commence par un négatif « au collodion humide », qui était la technique photographique utilisée à l'époque. Le négatif est placé sur une couche de gélatine bichromatée sèche et exposé au soleil pendant environ 60 minutes. Toute gélatine qui n’est pas exposée à la lumière via le négatif reste soluble dans l’eau et est simplement emportée par le lavage.
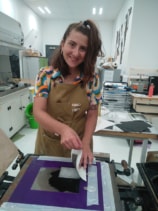
Le résultat est un relief 3D (un moule) incroyablement robuste de l’image, qui peut être pressé en plomb à l’aide d’une presse hydraulique. La plaque d'impression au plomb est ensuite huilée, remplie d'une gélatine tiède pigmentée de suie, et recouverte de papier avant de passer dans une presse à imprimer. Après environ cinq minutes, le papier est retiré et une fois l'encre sèche, l'impression est enfin aplatie et rognée. À l'origine, jusqu'à 10 plaques d'impression pouvaient être fabriquées à partir d'un seul relief de gélatine, et celles-ci pouvaient être montées dans un carrousel d'impression pour une impression de masse.
« Étant donné que les tirages Woodburytype sont basés sur de la gélatine pigmentée, ils sont entièrement archivables car la suie ou le noir de carbone sont extrêmement « résistants à la lumière » et la gélatine ne se détériorera pas ou ne changera pas chimiquement tant qu'elle n'est pas exposée à une humidité extrême », explique Klein. « Même si le processus initial prend beaucoup de temps et est devenu obsolète avec le décollage de la lithographie, la qualité de l'image est inégalée. Aujourd’hui encore, le Woodburytype reste la seule méthode de reproduction photomécanique en tons continus.
En revisitant la technique, Klein et ses collègues ont développé deux voies alternatives pour créer des imprimés Woodburytype avec des matériaux modernes. "Dans une méthode", explique Klein, "nous suivons le flux de travail d'origine, mais remplaçons la gélatine dichromatée par du photopolymère et le plomb par du silicium." De cette manière, le temps d'exposition est réduit de 60 minutes à quelques secondes, tandis que les plaques d'impression peuvent être réalisées en quelques heures plutôt qu'en quelques jours. Une méthode encore plus rapide utilise une découpeuse laser pour créer un relief en acrylique – produisant par exemple une plaque d'impression de 10 x 15 cm en 10 minutes. La précision de la découpe laser signifie également que les couches de cyan, magenta, jaune et noir nécessaires à la création d'images en couleur peuvent être facilement imprimées les unes sur les autres.
Les deux méthodes sont attractives pour les praticiens des beaux-arts pour la création d’œuvres d’art originales, mais elles sont également intéressantes pour les entreprises qui recherchent un moyen respectueux de l’environnement de créer des reproductions photographiques haut de gamme pour des installations artistiques et des publicités commerciales dans les espaces publics. Les avantages sont que la découpe laser des plaques d'impression est économe en énergie et ne produit presque aucun déchet, tandis que les encres sont à base de gélatine (un déchet de l'industrie de transformation de la viande). De plus, les impressions sont biodégradables et l'encre peut être éliminée du papier par lavage à l'eau.
Un autre domaine d'investigation Pour Klein, il s'agit de l'application industrielle de la « couleur structurelle », où la couleur n'est pas générée par des pigments mais par des motifs microscopiques réfléchissant et réfractant la lumière de manière unique (comme dans les ailes d'un papillon). Une option intéressante consiste à introduire des couches supplémentaires de cristaux liquides cholestériques (nématiques chiraux) dans le relief d’un type Woodbury, pour imprimer une couleur structurelle. Avec les matériaux appropriés, les cristaux liquides pourraient être orientés par la couche et les couleurs originales imprimées modifiées en appliquant un champ magnétique ou électrique, semblable à un écran bistable.
Les applications possibles incluent la lutte contre la contrefaçon pour l'étiquetage des produits de luxe, des créateurs de mode et des produits pharmaceutiques. « L'opportunité commerciale ici est importante », ajoute Klein. « Le défi est de produire des emballages sécurisés avec des encres d’imprimerie qui changeront de couleur à chaque fois qu’un article sera autorisé à différentes étapes de la chaîne d’approvisionnement avant d’être acheminé vers le client. »
Le scientifique des matériaux
Le collègue de Klein Nazmul Karim – responsable de recherche au sein du centre Laboratoire d'application du graphène – est un autre universitaire apparemment taillé sur mesure pour le creuset multidisciplinaire du CFPR. Avant de rejoindre l'UWE en 2019, Karim a passé quatre ans à travailler sur des vêtements fonctionnels hautes performances à base de graphène et des textiles électroniques portables (e-textiles) au sein de l'UWE. Institut national du graphène au Université de Manchester, UK.
Ses intérêts de recherche actuels – qui font partie des domaines de recherche du CFPR programme de nouveaux matériaux – inclure la préparation du graphène (via exfoliation et fonctionnalisation) du graphène et d’autres matériaux 2D pour les applications e-textile. Karim étudie également comment fabriquer des objets portables en graphène via des techniques de fabrication hautement évolutives telles que le revêtement et l'impression (c'est-à-dire avec des « encres » au graphène appliquées directement sur les textiles). « Mon équipe est passionnée par l'introduction de matériaux intelligents et d'intelligence artificielle dans l'électronique imprimée pour des applications de soins de santé personnalisées non invasives », explique Karim.

Les derniers résultats du groupe, basés en grande partie sur les travaux menés par un doctorant Md. Rashedul Islam, démontrent l’opportunité commerciale tangible qui se dessine. Islam a développé une plateforme de textiles électroniques polyvalente, entièrement imprimée, hautement conductrice, flexible et lavable en machine. Le matériau peut stocker de l’énergie à l’aide de supercondensateurs en graphène imprimés tout en surveillant une série d’indicateurs physiologiques, tels que la fréquence cardiaque, la température cutanée et diverses mesures d’activité. Ce qui est encore plus impressionnant, c'est que, lorsqu'il est transformé en un bandeau séparé, le prototype de textile électronique peut enregistrer l'activité cérébrale (un électroencéphalogramme ou EEG) selon les mêmes normes que les électrodes rigides conventionnelles. Pour le moment, les supercondensateurs sont chargés à l’aide d’une source d’énergie externe, mais l’objectif est de les rendre autosuffisants à l’avenir en introduisant une fonctionnalité de récupération d’énergie.
Le processus de fabrication exploite une technique de sérigraphie hautement évolutive, dans laquelle l'encre à base de graphène passe à travers un maillage conçu sur mesure sur un substrat textile rugueux et flexible. Les pistes conductrices sont ensuite encapsulées à des fins d'isolation et de protection, pour produire une plateforme de textiles électroniques lavable en machine. L'espoir est que des succès précoces comme celui-ci ouvriront la voie à la production en volume de vêtements e-textiles multifonctionnels à base de graphène, dans lesquels chaque vêtement dispose d'un réseau de capteurs portables et est alimenté par l'énergie stockée dans du graphène. supercondensateurs textiles.
Dans le même ordre d'idées, le laboratoire d'application du graphène étudie l'utilisation du graphène et d'autres matériaux fonctionnels (y compris les revêtements antimicrobiens) comme base de vêtements recyclables de haute qualité. À l’heure actuelle, environ 55 % des textiles sont fabriqués à partir de polyesters synthétiques – le plus souvent du polyéthylène téréphtalate (PET), qui n’est pas biodégradable et peut rester dans l’environnement pendant des centaines d’années. « Naturellement, les marques de mode et les détaillants s’intéressent de plus en plus aux tissus en polyester à base de polymère recyclé (rPET) avec un impact environnemental réduit », explique Karim.
Le problème est que les itérations actuelles de rPET souffrent du vieillissement thermique et se dégradent en raison d’un mélange aléatoire avec d’autres matériaux au cours du processus de recyclage. Il est encore tôt, note Karim, mais les premiers résultats du CFPR sont prometteurs, le rPET amélioré au graphène ayant déjà été transformé en fibres plus légères, mécaniquement plus robustes et plus faciles à recycler. « Ce sera un long jeu », ajoute Karim, « et nous aurons besoin d’une collaboration soutenue au sein de l’écosystème de l’innovation. Cela signifie que des groupes universitaires comme le nôtre travaillent main dans la main avec les fournisseurs de graphène, les fabricants de textiles et les grands détaillants de mode et de vêtements.
Le créateur de céramique
Une toute autre opportunité de fabrication préoccupe Tavs Jorgensen, potier artisanal et designer dans l'industrie de la céramique avant de poursuivre une carrière universitaire. Jorgensen est à l’avant-garde des efforts de R&D de CFPR en fabrication numérique, visant à accélérer l'application jusqu'à présent limitée des technologies d'impression 3D, de l'usinage contrôlé par ordinateur et de la robotique dans la production de céramique.
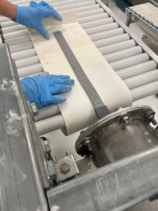
Jorgensen et son équipe s'intéressent particulièrement à un processus de production appelé extrusion. C'est à ce moment-là que l'argile molle et malléable est forcée à travers un canal, ou « matrice », qui confère une forme transversale particulière au matériau et donne une bande d'argile linéaire continue qui peut être coupée en morceaux pour produire des pièces individuelles telles que des briques. , carrelages, bardages et autres éléments architecturaux. Les extrudeuses industrielles sont utilisées pour fabriquer des pièces en céramique spécialisées, notamment des filtres pour pots catalytiques et des composants haute température pour fours et autoclaves. Parallèlement, les systèmes d'extrusion manuels sont souvent utilisés dans les ateliers d'artisanat pour créer des poignées et des éléments décoratifs uniques en soutien à d'autres méthodes de production telles que le pressage et le moulage. "Notre défi", explique Jorgensen, "est de savoir comment exploiter les technologies numériques et la robotique pour étendre les utilisations actuelles de l'extrusion d'argile à des applications commerciales et de conception plus innovantes."
Le paramètre par défaut de l’équipe repose en grande partie sur des expériences pratiques. « Parfois, les tests sont effectués sous forme d’explorations ouvertes aux résultats très imprévisibles, une approche largement motivée par la curiosité – que se passe-t-il lorsque nous faisons cela ? Les connaissances fondamentales sur la physique et les matériaux sont un élément important pour comprendre le comportement de l'argile. Par exemple, pendant le séchage et la cuisson, les morceaux d'argile extrudés rétrécissent d'environ 10 à 15 % et peuvent se plier et se fissurer en raison des tensions résultant du processus d'extrusion.
"La nature de l'extrusion d'argile rend les calculs théoriques du résultat difficiles", explique Jorgensen, "bien que des travaux aient été réalisés pour développer des algorithmes pouvant aider à prédire l'écoulement de l'argile dans une situation d'extrusion." Dans le cadre d'un rapprochement interdisciplinaire opportuniste, Jorgensen s'est tourné vers l'expertise de Damien Leech – un ancien physicien théoricien du CFPR désormais basé au centre belge de nanoélectronique imec – développer des modèles prédisant comment certaines géométries de filières pourraient affecter les pressions nécessaires à l’extrusion de l’argile. "Bien que les tests empiriques restent la méthodologie de base des enquêtes", ajoute Jorgensen, "la modélisation théorique s'est révélée inestimable, fournissant une compréhension de base des géométries qui seraient les mieux déployées dans les expériences physiques réelles."

L'équipe crée également des flux de travail d'outillage qui permettent de prototyper et de tester rapidement de nouvelles conceptions de matrices pour l'impression 3D, ce qui ouvre la voie à des applications pour l'extrusion de céramique dans des applications industrielles de haute performance. Au premier plan se trouve la collaboration R&D de CFPR avec le Centre National des Composites (NCC) à Bristol. Ils s'intéressent au potentiel d'extrusion de composites à matrice céramique (CMC), une classe de matériaux dans lesquels de la pâte céramique est mélangée à des liants inorganiques pour augmenter la ténacité à la rupture sous charge mécanique ou thermomécanique.
Les partenaires CFPR/NCC définissent et itèrent actuellement les détails du processus, y compris les outils de support, les gabarits, les composants et les flux de travail. Cependant, à long terme, ils envisagent toutes sortes d'applications dans des secteurs tels que la production d'électricité et l'aérospatiale, où les CMC sont de plus en plus utilisés pour les systèmes de protection thermique à haute température. "L'extrusion est une manière entièrement nouvelle de produire des CMC", explique Jorgensen, "et cette recherche nous ouvre la possibilité de créer des pièces en CMC avec des géométries exotiques, telles que des tuyaux et des profilés dotés de structures internes complexes." De tels tuyaux en CMC suscitent l'intérêt pour la prochaine génération de centrales nucléaires, tandis que le processus d'extrusion a le potentiel de soutenir l'objectif de zéro carbone net du Royaume-Uni pour les matériaux de construction, Jorgensen et ses collègues explorant l'extrusion d'argile non cuite et de mélanges de fibres pour des matériaux à faible teneur en carbone. composants de construction en carbone.
Un état d'esprit ouvert et ouvert aux affaires
Si la convergence, la collaboration et la co-création sont fondamentales pour le modèle de recherche du CFPR, le mélange d’artistes, de designers, de scientifiques et de technologues du centre, travaillant dans les disciplines de l’impression traditionnelle et numérique, l’est également.
Le groupe rassemble également des personnes d’horizons divers, avec des chercheurs issus de l’industrie et du monde universitaire. Ce mélange d’expertise et d’expérience soutient les vastes collaborations universitaires et industrielles internationales du CFPR ; avec des partenaires commerciaux, notamment des imprimeries spécialisées, des fabricants de céramique et des entreprises technologiques multinationales. Les projets communs de R&D vont de la recherche contractuelle ciblée et des études de faisabilité au co-développement de matériaux, de processus et de systèmes d'impression complets avancés.
Il est évident qu’il n’existe pas de règles strictes en matière de collaboration au CFPR, mais plutôt des variations sur un thème dans lequel la pensée ouverte d’esprit se mêle à la créativité, à l’innovation scientifique et technologique dans les pratiques d’impression avancées.